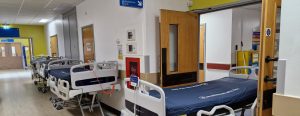
Product Standardisation Advantages
Product standardisation has a number of key advantages when old hospital equipment is replaced with new. This post looks into the practical aspects of standardising products, and how it can offer significant benefits to both staff and patients.
Introduction
An efficient way to swap old beds and mattresses for new is to do a large-scale hospital-wide replacement. This is often referred to as an ‘implementation’.
We completed a research study in 2024, looking at large-scale implementations of Medstrom beds and mattresses, from NHS staff who had played a key role.1 The overall aim was to provide practical suggestions, advice and tips to NHS managers who are planning a similar project.
The research involved semi-structured interviews, in which the whole implementation project was discussed, from planning to execution and beyond. From this, some interesting feedback about the need/wish for product standardisation came out. This post discusses these findings, along with supporting background information.
Change Drivers
We asked study participants about the main drivers for change which ultimately led to the decision to replace a large number of beds and mattresses at once. These naturally split into two categories – necessity and desire for positive outcomes:
Necessity
- Old products frequently breaking down.
- Cost of repairs and replacements.
- Unsupported products – e.g. spare parts unavailable/expensive.
- No storage space for broken equipment.
Desire for Positive Outcomes
- Improve staff wellbeing – e.g. time savings, reduction in manual handling risks.
- Improve patient outcomes – e.g. reduce falls and pressure ulcer incidence.
- Product standardisation.
Standardising new products across a Trust plays a key part in meeting the rest of the change drivers listed above.
Old and Faulty Equipment
Older medical devices are more likely to malfunction.2 Additionally, 25–35% of equipment ‘down time’ is caused by the absence of preventive maintenance, inability to conduct repairs, and lack of spare parts.3
Replacing old, faulty products with new solves many of the problems which the old ones create. For example, new products are much less likely to break down. Even if they do, or if hospital-acquired damage occurs, spare parts are much more accessible.
Product standardisation can greatly reduce the number of spare parts needed, and the associated costs. For example, a new bed, implemented hospital-wide, has one set of spare parts, as opposed to five old beds with five times the amount. As a result, less storage space is needed, and fewer parts, due to reduced breakdowns.
New products are much better supported – via warranty, managed services (e.g. total bed management), and planned preventative maintenance programmes.
Medstrom, being a UK manufacturer, holds spare parts in the UK, so they are available locally and quickly, even if a hospital runs out. This is in sharp contrast to waiting weeks or even months for spare parts to arrive from overseas.
Staff Wellbeing
Standardising new products can help improve staff wellbeing in a number of ways:
- Easier training. A hospital may have three or four old med/surg bed models in its fleet, bought at different times from several suppliers. So staff would need to know how to use all of these. In contrast, replacing them with one new model reduces the training burden.
Human error reduction. Having less products to learn and remember how to use reduces the risks of mistakes. This can then have a positive effect on morale.
- Reduced manual handling risks. Some old hospital beds are difficult to move and push, caused by a combination of overall weight and castor degradation. New beds are likely to be lighter and easier to push. In addition, features such as an improved bed height range can help reduce caregiver injury.
- Time savings. Fewer breakdowns will free up time for technical staff, and for clinicians who would otherwise need to source a replacement product and move the patient onto it.
Patient Outcomes
Because of risks to patients and staff from faulty or outdated equipment, the Care Quality Commission requires healthcare providers to ensure that their equipment is fit for purpose, properly used and maintained, and meets the latest regulatory standards.4,5
Patient outcomes can be negatively affected by faulty equipment. For example, a defective bed side rail can result in patient entrapment or falls,6 and over-inflated or ‘bottomed-out’ mattresses can result in pressure injuries.7,8
Replacing old beds and mattresses with standardised new products will mitigate these risks, which should in itself help to improve patient outcomes. But new, standardised products can also provide new benefits across the board. For example:
Has an ultra-low platform height of 21cm, helping to reduce the risk of injury from falls. Implementing Solo+ hospital-wide ensures that every patient who needs a low bed gets one.
- Has an elliptical backrest movement, which mimics spine elongation when a person goes from a lying to a sitting position. This stops heel travel and the associated shear and friction, helping to reduce pressure ulcer risk for all patients using the bed.
Suitable for very high risk patients and up to Category 4 pressure ulcers. This reduces the need for ‘step up’ to another surface in a lot of cases, and ensures that at risk patients are on the best surface early, for optimal pressure area care.
- Can be ‘stepped up’ by simply adding a control unit. As well as saving time, it ensures the patient is receiving the right therapy at the right time.
If you are thinking of replacing old products and have any questions, please feel free to contact us. Our experienced team are always here to help.
References
-
Martindale, D & Allan, L. Large-scale acute hospital bed and mattress implementations: insights and recommendations. British Journal of Healthcare Management. 2024. https://doi.org/10.12968/bjhc.2024.0072
-
Seo G, Park S, Lee M. How to calculate the life cycle of high risk medical devices for patient safety. Front Public Health. 2022;10;989320. https://doi.org/10.3389/fpubh.2022.989320
-
Sandham J. Medical equipment procurement and management issues. 2013. https://www.ebme.co.uk/articles/management/medical-equipment-procurement-and-management-issues
-
Care Quality Commission. Taking action. 2023. https://www.cqc.org.uk/about-us/how-we-do-our-job/taking-action
-
Care Quality Commission. Regulation 15: premises and equipment. 2023. https://www.cqc.org.uk/guidance-providers/regulations/regulation-15-premises-equipment
-
Medicines and Healthcare products Regulatory Agency. National patient safety alert: medical beds, trolleys, bed rails, bed grab handles and lateral turning devices: risk of death from entrapment or falls (NatPSA/2023/010/MHRA). 2023. NatPSA_bed_rails_30_8_23.pdf
-
Ovens L. Selecting a support surface. 2017. https://wounds-uk.com/how-to-guides/how-to-guideselecting–a-support-surface/
-
Aria ON, Gbeneol JT. The static air-mattress-inflation pressure and nosocomial pressure injury – an innovation in preventing pressure injuries. Clin Res Open Access, 2021;7(2). https://doi.org/10.16966/2469-6714.167